Din 2391 Cold Drawn Seamless Precision Steel Tube Manufacturers
-
2022-11-03
-
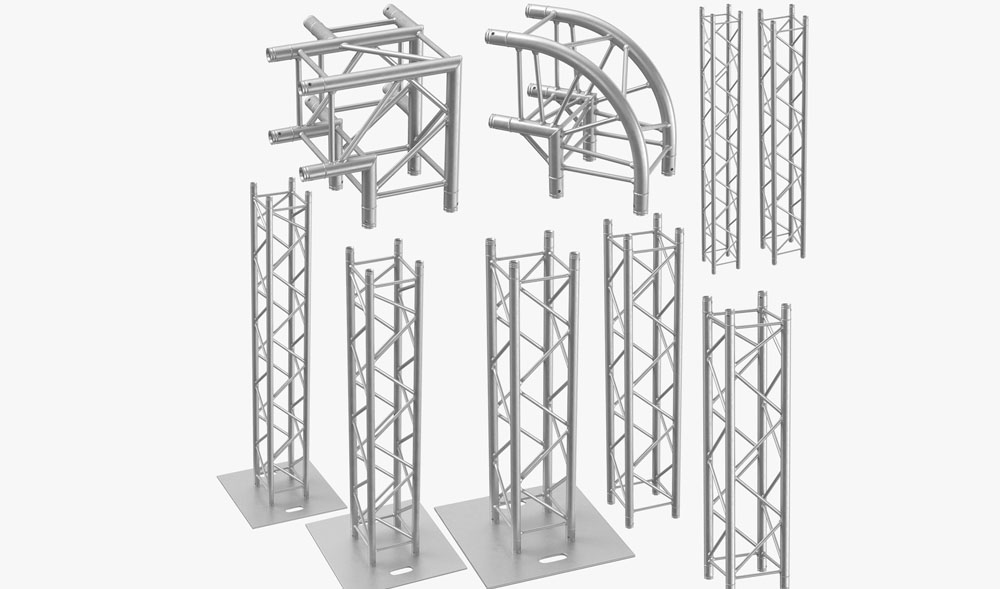
Precision tube manufacturing involves the production of tubes that are consistently round and smooth, with little deviation from the ideal dimensions. The practice has become increasingly necessary due to the growing demand for smaller, more compact machines and devices. As a result, many precision manufacturers have begun investing in more advanced equipment, such as laser-based measurement systems, to reduce the risk of defects in their finished products.
Types of precision tubes
There are several types of precision tubes used in different industries. The following are the most common: • Precision tubes used in medical equipment like syringes, needles, or catheters have very consistent diameters and are used for precise fluid transfer. • Laboratory equipment and scientific instruments are often built with cylindrical or tubular components that are very smooth and round. • Aerospace components and engine parts are made from tubes with very consistent wall thickness and dimensions. • Communication devices like fiber optic cables and microwave waveguides are often made from a tube made from a single piece of metal.
Why is manufacturing precision tubes important?
Precision tubes are an important part of many industries, including laboratory, medical, and aerospace. There are a number of reasons why these types of tubes are important. – Medical tubing – Medical tubing is often manufactured using precision tubes to ensure that the diameter is consistent and that there is little risk of contamination due to a porous material. Precision tubes are also necessary when a sterile seal is required, such as in blood bags and IV tubes. – Laboratory equipment – Laboratory equipment is often built using precision tubes to ensure that the tube is smooth, round, and that the wall thickness is consistent throughout the entire tube. This can help prevent leaks and ensure that the equipment works as expected. – Aerospace components – Aerospace components often require the use of precision tubes to ensure the structure of the aircraft is sound. Tubes are often used to transfer fluids and gases to and from the aircraft and at times, even as a part of the aircraft structure.
Benefits of using advanced equipment while manufacturing tubes
There are several benefits of using advanced equipment while manufacturing tubes. These include: – Consistent wall thickness – Advanced equipment can be used to ensure that the wall thickness is consistent throughout the entire length of the tube. This can help prevent the tube from being too thin at one point and being too thick at another. – Roundness – Advanced equipment can be used to ensure that the tube is round and smooth, without any dents or dings on the surface. This helps to avoid defects in the finished product and reduces the risk of a tube bursting during use. – Precision – Precision is one of the most important aspects of manufacturing tubes. Advanced equipment can be used to ensure that the dimensions and dimensions are consistent along the entire length of the tube.
Requirements for advanced equipment in the production of precision tubes
There are a number of requirements that must be met when it comes to selecting advanced equipment for the production of precision tubes. – Accuracy – Tubes are often manufactured as a single piece of metal, which is why accuracy is an important factor. – Repeatability – The equipment used to manufacture precision tubes must be able to produce the same results over and over again. This ensures that all of the tubes have the same dimensions. – Ruggedness – The equipment used to manufacture precision tubes must be able to stand up to the rigors of everyday use. This can help extend the life of the equipment and keep maintenance costs low.
Lasers as measurement tools during tube manufacturing
Lasers are often used to measure the inside diameter and wall thickness of a tube during the manufacturing process. This helps to ensure that the tube is consistent throughout. – Laser inside diameter measurement – Inside diameter measurements can be taken with a laser inside diameter measurement tool to ensure that all of the tubes contain the same internal diameter. – Laser wall thickness measurement – Wall thickness measurements can also be taken with a laser wall thickness measurement tool to ensure that all of the tubes have the same wall thickness. – Laser tube length measurement – Laser tube length measurement tools can be used to make sure the tube is the desired length.
Advantages and disadvantages of laser measurement tools during tube manufacturing
There are several advantages and disadvantages of using laser measurement tools during tube manufacturing. Advantages Disadvantages
Conclusion
Precision manufacturing is important in many industries, including medical, laboratory, and aerospace. There are several types of precision tubes that are necessary in these fields. Advanced equipment can be used to ensure that the tubes are round and smooth with consistent wall thickness and a consistent diameter. Lasers are often used to measure the inside diameter and wall thickness of the tubes. There are several advantages and disadvantages of using laser measurement tools during tube manufacturing.