Din 2391c Precision Seamless Steel Tube
Product Description
Din 2391c Precision Seamless Steel Tube is a high-quality carbon steel tube used primarily in hydraulic and mechanical applications. It offers excellent dimensional accuracy and surface finish due to its precision manufacturing process. Designed for high pressure and demanding conditions, this tube is ideal for a range of industrial and engineering applications.
Product Advantages
Materials
- The material used for this tube is high-quality carbon steel, with the precise alloy composition ensuring excellent mechanical properties, such as strength, durability, and high pressure resistance. It also provides good weldability and formability.
International Standards:
- DIN 2391/C(German Standard)
- EN 10305-1(European Standard)
These international standards ensure that the tubes meet consistent quality and performance levels, suitable for global applications.
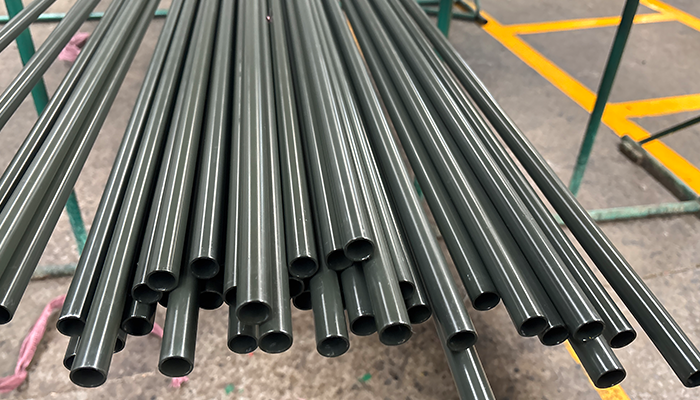
Dimension
Specification | Details |
Material | Carbon Steel (St37.4) |
Standard | DIN 2391/C, EN 10305-1 |
Surface | Corrosion-resistant oil coating, optional phosphating or plating |
Delivery State | Cold Drawn, Annealed or as per requirement |
Dimensions:
Dimension | Range |
Outer Diameter (OD) | 6mm – 150mm |
Wall Thickness (WT) | 0.5mm – 12mm |
Length | 6 meters (custom lengths available) |
Features
-
- Precision Manufacturing: The cold-drawn process ensures high dimensional accuracy and smooth internal and external surfaces.
- High Strength: The tube is made of high-quality carbon steel that offers exceptional tensile strength and resistance to mechanical stress.
- Corrosion Resistance: Tubes can be treated for enhanced corrosion resistance, making them suitable for various harsh environments.
- Seamless Design: The seamless structure ensures better reliability and avoids issues like seam defects which can occur in welded tubes.
- Surface Finish: Smooth surface finishes, especially after cold drawing, allow for better fluid flow in hydraulic systems, reducing friction and wear.
Surface:
- Standard: The tube typically comes with a corrosion-resistant oil coating on both inner and outer surfaces to protect against rust during storage and transportation.
- Optional Surface Treatments: Additional treatments like phosphating, chrome plating, or passivation can be applied depending on specific requirements for anti-corrosion and durability.
Manufacturing Process
- Piercing: A solid steel billet is first pierced to create a hollow tube.
- Cold Drawing: The tube undergoes cold drawing to achieve precise dimensions and smooth surfaces.
- Annealing: The tube is annealed to relieve internal stresses created during the drawing process.
- Surface Treatment: After drawing and annealing, the tube may undergo surface treatments such as phosphating or zinc coating to enhance corrosion resistance.
- Inspection: The tube is thoroughly inspected for dimensional accuracy, surface quality, and mechanical properties.
Applications
- Hydraulic Systems: Widely used in high-pressure hydraulic systems such as in machinery, construction equipment, and automotive applications.
- Mechanical Engineering: Suitable for mechanical applications where high precision and strength are needed, such as in pumps, compressors, and pressure vessels.
- Automotive: Used in hydraulic braking systems, power steering systems, and fuel systems in vehicles.
- Industrial Machinery: Ideal for use in manufacturing equipment and heavy-duty machines that require high-quality, high-pressure steel tubing.