Advantages of Electronic Welded Seamless Steel Tubing
-
2022-09-07
-
What Is Electric Resistance Welded Seamless Steel Tubing?
Electric resistance welded seamless steel tubing is a seamless pipe made by the electric resistance welding process. We commonly use it in mechanical and chemical industries, as well as in piping systems for water supply and drainage.
Electric resistance welded tubing belongs to the category of seamless pipe. It has good corrosion resistance and can be used in various media with high temperatures or corrosive environments. The advantages of electric resistance welded tubing include large inside diameter and small wall thickness, which lead to its low weight and high strength compared with other types of seamless pipes, such as welded steel pipe and seamless steel tube. Electric resistance welded tubing also has good chemical and physical properties, such as high strength, good impact toughness and excellent chemical stability at high temperature.
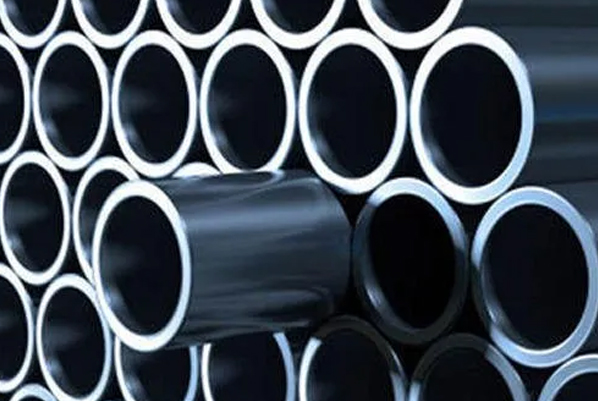
Electric Resistance Welded Seamless Steel Tubing
Benefits Of Electric Resistance Welded Tubing:
1. Electric resistance welded tubing has high quality and excellent performance and is widely used in the oil and gas, chemical industry and construction engineering.
2. The electric resistance welded tubing is good for the environment, with no fumes or odours during the working process, so it is safe for human health.
3. We can customize it according to your request, which makes the products more beautiful and more fit for the customer’s market requirements.
4. Electric resistance welded tubing has a long life span, which also means that it will save your cost in long run.
5. Cost Effective: Electric resistance welded tubing is one of the most cost-effective methods for joining two different types of materials together. The process uses a high-frequency current to heat up the end of the tube is welded and then pressure is applied by means of mechanical force. This type of welding is also speedy, which makes it ideal for large-scale construction projects where time is money.
6. Creates an Even Seam: The process creates an even seam that has no weak points where leaks may occur over time due to corrosion or other factors. The seam created with this method is stronger than the material itself, making it ideal for underground pipes that are subjected to harsh weather conditions such as freezes and thaws during the winter months.
7. No Welding Flux Required: There’s no need for flux when using this method because there is no melting involved with this type of welding process.
Features Of Electric Resistance Welded Tubing:
1) The thermal conductivity of the electric resistance welded tube is higher than that of conventional pipe. Therefore, the heat transfer coefficient is higher than that of the same type of steel pipe.
2) Electric resistance welded tube has excellent corrosion resistance and good hydrogen embrittlement resistance. You can use it for long-term service under the action of high-temperature water vapour or steam in oil refineries, chemical plants and other industries without any problems.
Applications:
The electrical resistance welding (ERW) process starts with a copper wire, which is fed through the tube to be welded. The wire is then powered using alternating current, which heats the material and causes it to contract. This creates a void where the two pieces of metal are joined together. The void is then filled with molten metal by using a filler rod. The filler rod continues to feed into the tube until it reaches the end of the tube or until there is no more room for it to enter.
The process of resistance welding can be used to create seamless or welded tubes in any size or shape required for use in industrial and commercial applications.
- 1. Power transmission and distribution:
Electric resistance welded tube is mainly used in power transmission and distribution, especially in the field of high-voltage transmission lines, as well as low-voltage distribution lines.
- 2. Water supply and drainage:
In the water supply and drainage industry, we often use it especially for underground water pipes, which can withstand high pressure.
- 3. Gas pipelines:
You can also see it in gas pipelines such as natural gas pipelines and oil pipelines. The corrosion resistance of electric resistance welded tube is superior to that of carbon steel pipe, so it is suitable for use in corrosive environments such as seawater or brine-containing water sources.
- 4. Chemical industry:
We often use it in the chemical industry, such as ammonia or hydrogen production plants.
Corrosive gases will be generated during operation, quickly corrode ordinary steel pipes, but electric resistance welded pipes are very resistant to this type of corrosion. Because seam welding technology can effectively protect the inner wall of the pipeline from corrosion caused by erosion and wear during operation.
Why Choose Global Steeltube For The electric Resistance Welded Tubing?
Global Steeltube is one of the leading manufacturers and suppliers of electric resistance welded tubing. We offer a wide range of products, including carbon steel pipes, stainless steel pipes, copper tubes and so on.
The main feature of our electric resistance welded tubing is high strength and pressure resistance. The electric resistance welded tubing has good mechanical properties such as high-temperature strength and toughness etc. This kind of tube has good corrosion resistance in the soldering and welding process. We use it for pressure vessels, heat exchangers, chemical reactor equipment etc.
1. Customized Electric resistance welded tubing
2. Competitive price and good quality
3. Prompt delivery time
- Experienced factory and professional staff
- Low price and high quality;
- High strength;
- Abrasion resistance;
- Easy processing;
- Good appearance quality, no burrs on the surface of the product.
Precautions:
In order to ensure the quality of the product and customer satisfaction, we have introduced the following precautionary measures:
1) In the process of welding, we use a nitrogen gas purification system to remove oxygen from the welding area, which can effectively reduce the possibility of oxide film on the weld surface.
2) We also use high-quality welding electrodes with high purity and low carbon content, which can effectively improve weld quality.
3) Clean the surface with a clean solvent before welding.
- To ensure that each piece of tubing has no damage or defects before delivery, we will conduct internal and external visual inspections according to our company’s specifications.
- Observe the following precautions when using resistance welded tubing:
- Avoid contact with the stainless steel surface. After touching it, then wipe it off immediately.
- Do not use abrasive cleaners on the stainless steel surface.
4) Do not use chlorine or alkaline detergents for cleaning or rinsing after welding.
- Use welding gloves when handling it in order to avoid injury due to heat and abrasion
- Do not allow oil or grease to enter into the water-cooled welding zone during operation (this may cause electrical leakage and arc breakdown).
Conclusion:
The resistance welded tubing is a relatively new product in the market. However, many users has accepted it due to its excellent performance, high quality and reasonable price. The resistance welded tube has many unique properties and advantages in comparison with other processes of tube manufacturing.
It consists of two or more layers of steel strips welded together by heating and applying pressure so that we can make them into a single tube. This process requires no expensive equipment or special skills, which makes it suitable for small-scale production plants.
The advantages of resistance welding include:
1) It’s easy to learn;
2) It’s cheaper than other processes;
3) It doesn’t require any special equipment;
4) It doesn’t require skilled operators.
If you are still have problems when selecting, please contact Global Steeltube. It is our honour to be able to help you answer your questions!